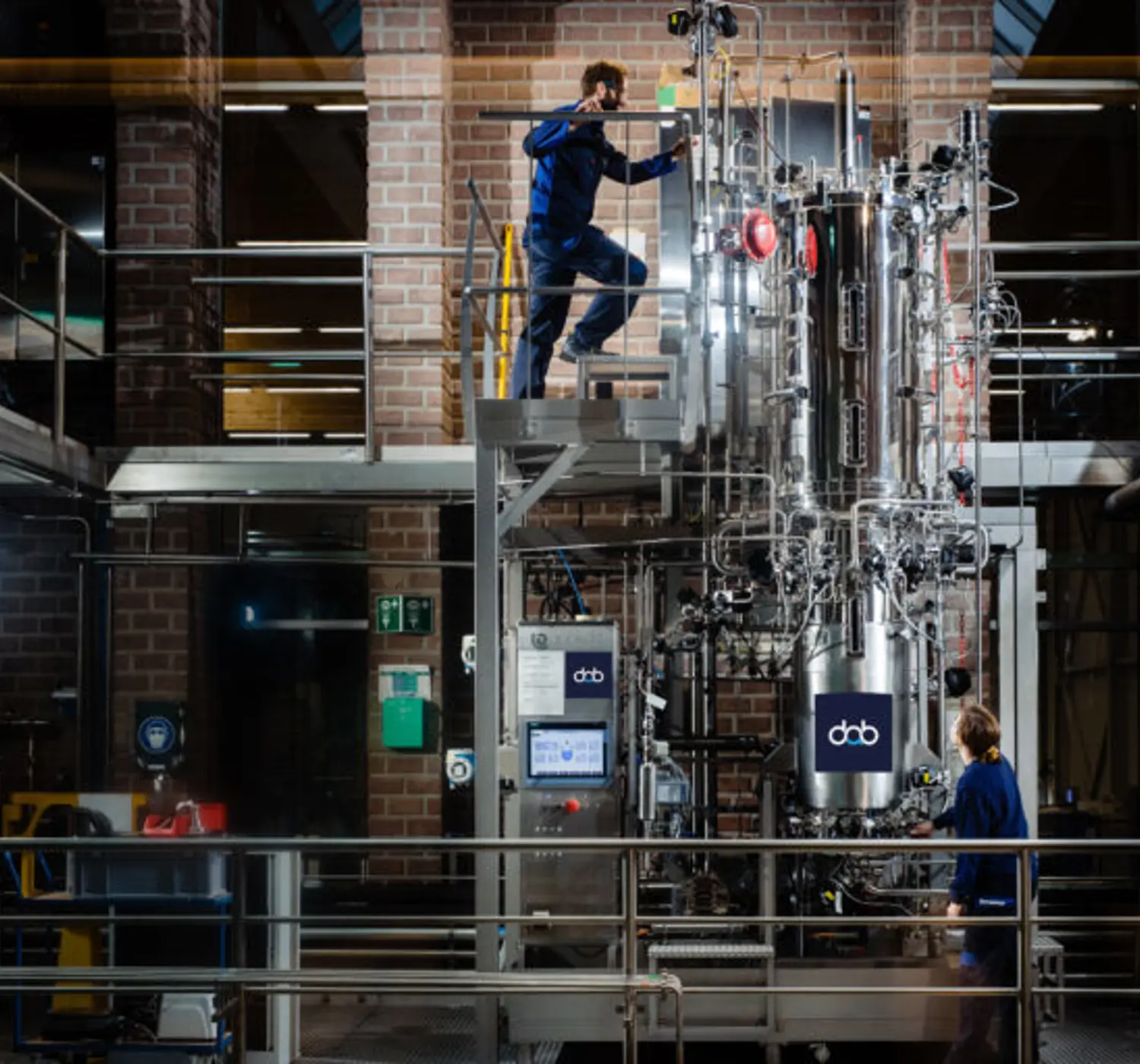
Finally, DAB.bio’s manufacturing breakthrough makes it viable to replace fossil fuels in manufacturing.
DAB.bio, pioneers in biomanufacturing fermentation technology, today announced successful fermentation runs in their FAST (Fermentation Accelerated by Separation Technology) bioreactor, demonstrating that the technology lowers the unit cost of fermentation-based production at scale. Using FAST to produce fermented compounds promises to enable higher market shares for biobased ingredients used in everyday products, thereby reducing societies’ dependence on fossil-based chemicals.
FAST dramatically increases fermentation performance and lowers product costs by continuously removing product from the fermenter. This boosts the amount of product formed and simplifies the purification process and the amount of equipment needed. With existing technology, fermentation and extraction are successive steps and require additional, often expensive and cumbersome equipment. By increasing fermentation-based production by up to tenfold, the technology reduces production costs by 50% and promises to drive higher margins for bio-products worldwide. The technology can also enable the production of completely new and sustainable compounds made using synthetic biology. Industries served include flavors and fragrances, food, nutraceuticals, natural insecticides, pigments, and specialty chemicals.
“We believe the real change in biomanufacturing can only occur by combining biology with radical process improvements - whatever synthetic biology can make, we can make cheaper,” said Eric van der Meer, Chief Executive Officer at DAB.bio. “With 10 years of R&D, DAB.bio has developed the first technology platform that addresses the world’s need for enormous amounts of fermentation capacity. The success of FAST, which we are making available to all biomanufacturers, is the catalyst for a scale-up across the industry.”
FAST in Operation
Bio Base Europe Pilot Plant (BBEPP) currently houses DAB.bio’s demonstration fermentation unit of 500L (FAST500) which is available to biomanufacturers that want to prove economic viability of their compounds at scale. DAB.bio’s proprietary hardware, built in less than 12 months, integrates production and recovery of a wide range of biobased products.
Nico Snoeck, Business Development Manager at Bio Base Europe Pilot Plant states, “We are very pleased with this exciting partnership. Together with DAB.bio, we realized the commissioning of this new installation in a minimum amount of time, and the first trial runs were immediately successful. It’s an amazing achievement! As a multipurpose pilot facility BBEPP can now offer customers DAB.bio’s FAST technology, in addition to our regular services, so they can compare the benefits of FAST versus classic fermentation technology for a wide range of processes and subsequent downstream processing steps.”
Since completion of the hardware, DAB.bio has successfully completed four out of four runs with three different products:
- Butanol - a base chemical used in a variety of applications ranging from spandex to paint thinner and to jet fuel.
- A roses-smelling alcohol for use as an antimicrobial, antiseptic, and disinfectant that is used also as an aromatic essence and preservative in pharmaceutics and perfumery.
- A terpene compound used in essential oils, as an insect repellant, and in diesel.
These runs demonstrate how DAB.bio’s game-changing fermentation technology, which can be scaled up quickly and easily, transforms the economics of bio-manufacturing. The innovative technology allows for long-duration fermentations and efficient separation of the product into a concentrated stream.
The demonstration plant confirms that industrial production of a diverse range of bio-compounds can be cost-effective at scale. Instead of having to recover a few kilograms of product from the entire fermenter volume, with FAST, the same quantity of product (often much more) is continuously extracted from the fermenter into a volume 10x smaller. This super concentrated product is available in real-time with fewer successive processing steps to make the final product. The newly installed hardware can be used as a stand-alone 500L bioreactor for process design and optimization, or operated in conjunction with a 15m3/15000L BBEPP fermenter, allowing for commercial sample production.